Our Capabilities
in Engineering
BW Design Group’s engineering services were built to scale and flex to the needs of our clients across markets. As an engineering-led organization, our technical experts and engineers enable us to develop and execute customized solutions that deliver on our clients' commercial goals with agility, efficiency, and creativity.
- #101 ENR Top 500 Design Firms
- #63 ENR Top 100 Design-Build Firms
- #8 System Integrator Giants
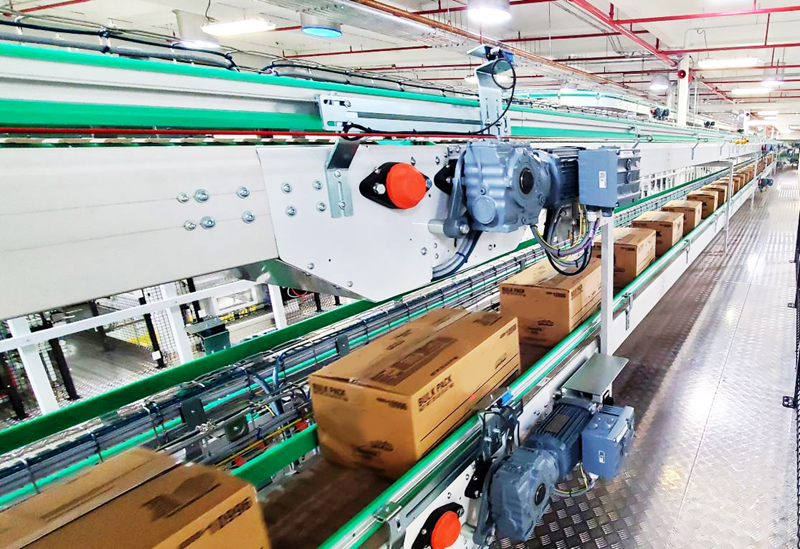
Our Team
Engineering
Leaders
Our Engineering Capabilities
Facility Engineering
As the only firm born from a manufacturing technology company to become an independent and fully integrated firm, we think like our clients think. We combine deep domain expertise in the manufacturing environment with an approach that is customized to realize the commercial impact and return on capital investment our clients seek.
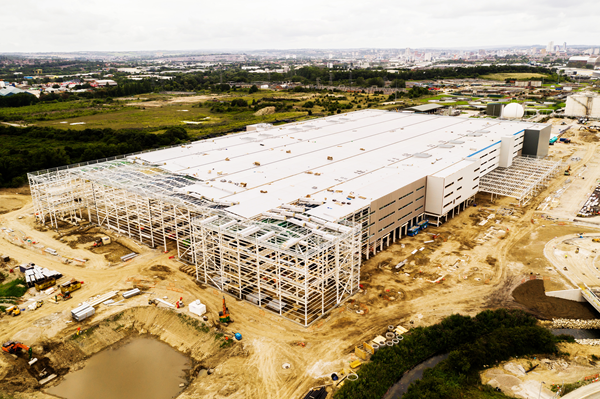
Process Engineering
Whether adding manufacturing capacity, addressing product quality, efficiency and yield, or introducing a new product to the market, BW Design Group understands what it takes to successfully design, integrate, and implement a new or modified process solution. Our deep domain expertise and seasoned experts deliver world-class, high-performing solutions that enable our clients to be future-ready.
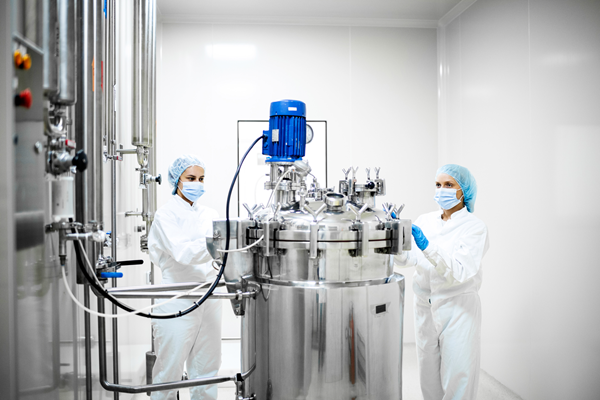
Packaging Engineering
As a leading system integrator for a wide range of filling and packaging line solutions, we provide complete production systems, line upgrades or experienced professionals ready to complement our client’s project team. Our professionals apply their broad packaging system knowledge with industry-leading technologies and best practices to specify and implement total operational solutions to meet the client’s specific needs.
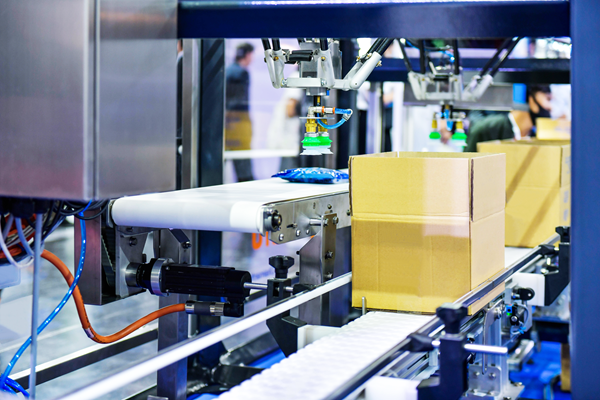